Matthew Barra, Liquor Cabinet with Sliding Tambour Doors (Student Awards 2019)
Liquor cabinet with sliding tambour doors, metallic epoxy resin inlay and purpleheart dovetail keys. For my Year 12 Industrial Technology – Timber Products and Furniture Technologies course, I was required to test, learn and display skills in craftsmanship by designing and manufacturing a fully functional and aesthetically pleasing major project that explores various woodworking techniques and joinery to meet the specified criteria provided. However, when determining firstly what product I should make and secondly which specific details and specifications were required to meet this criteria, I realised the majority of students have a similar theme in their major projects. This theme being that students of past and present tend to have common projects e.g. jewellery boxes / coffee tables and common joinery techniques such as dovetails / rebates. So this got me thinking. I asked myself “how can I manufacture a product that stays true to skilfull craftsmanship yet be completely unique in as many details as possible”. After doing some research on furniture products of both the emerging new trends and the more retro appearances, I came across many minimalistic and sleek cabinet designs but most importantly, I came across a fascinating old roll-top desk. This desk inspired me to come up with something unique by combining the old with the new, which I believed I have achieved. In order for me to have achieved my goal of being unique yet still meeting specified criteria, I used a number of thoroughly chosen techniques, processes and materials throughout my project. The main techniques used throughout my project include housing joinery for the general construction of the carcase, sliding rebate joinery to act as a track system for the doors to operate smoothly, the inlaying of contrasting timbers throughout my drawers and a twist on conventional dovetail joinery but instead dovetail-key joinery. The key processes used throughout my project include flocking of the drawer bases, an epoxy resin inlay mixed with a metallic blue pigment in order to create a flowing river effect, tambour doors initially being individual strips then attaching them together with a heavy duty fabric, the creation of jigs mainly for both tambour door and dovetail-keys, edgebanding to clean up the edges of material and both CAD / CAM (Computer Aided Design / Computer Aided Manufacturing) through the use of a CNC router. The materials used in my case can be considered unique as it is thought that in order to have a high quality product, you need to used solid timber as your core material however I had chosen to use spotted gum veneered BB hoop pine plywood sheeting for my main material as it allowed me to save money, time and weight due to the advantages of manufactured boards over natural timbers. The veneered plywood was used for the general construction of the carcase and the doors. I have used other materials such as a live edge tallowwood slab for the feature top as I wanted to take advantage of the natural shape of the live edge to replicate a river. I also used the exotic and imported timber, purpleheart for my dovetail-key joinery and inlay on the drawer face. The other main materials used are not timber products and they include West Systems 105 Epoxy Resin for the feature top and weatherproof canvas to hold the strips in the door together. The overall construction of my major project was difficult, confusing, tedious and at times mentally and physically straining but now seeing the finished product… it's extremely rewarding and most importantly 100% worth it! There were many ups and downs, many things going to plan and many more things not. I believe this wasn’t because of a lack of research but more because I was exploring lots of new techniques and processes I’ve never attempted before or not know how to completely do them right e.g the resin inlay for my feature top cracked not once but twice, or trial and error with the dovetail-keys. I’d be the first to admit this project has many mistakes as I am inexperienced and they are essentially inevitable to happen but I believe it is the ability of a woodworker to hide their mistakes to the best they can is what makes them a talented woodworker/craftsman. So with that said I’d like to thank my teacher Mr Stephen Bushell and my father / talented joiner for all the incredible support and constant guidance provided to me throughout the creation of my major project. Year 12, Gilroy Catholic College. Teacher: Stephen Bushell
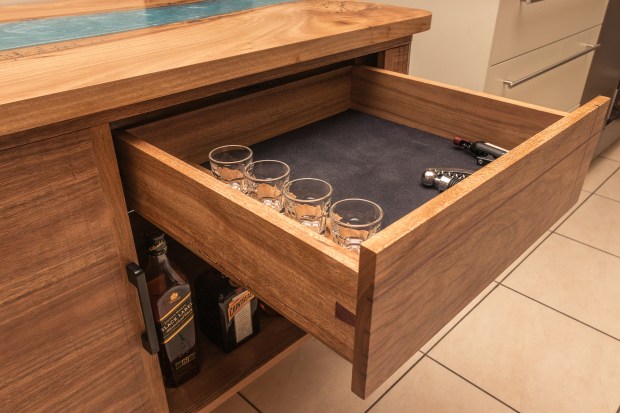
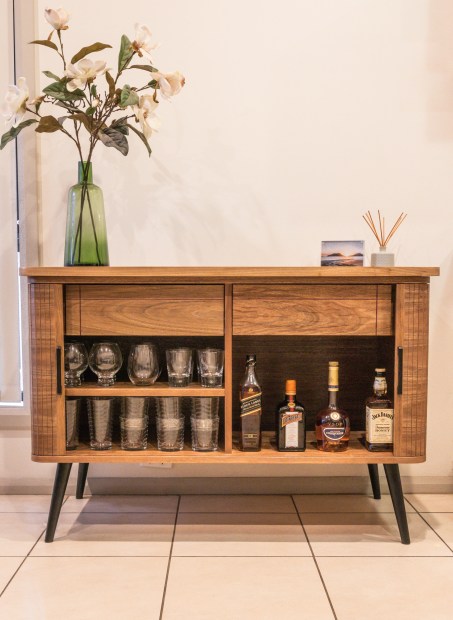
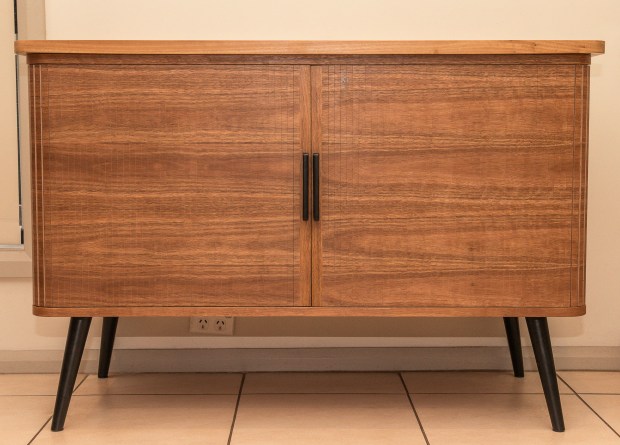
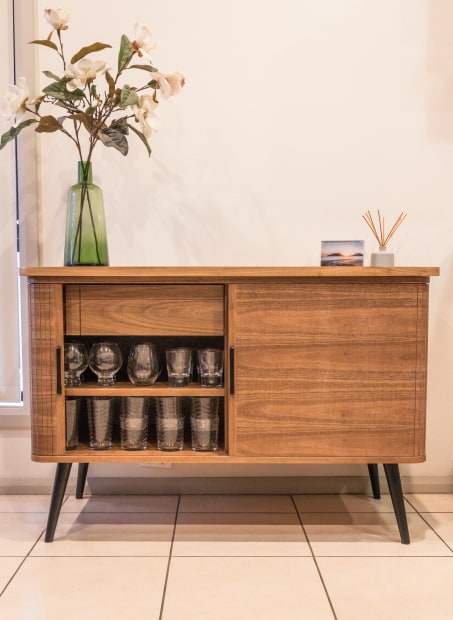
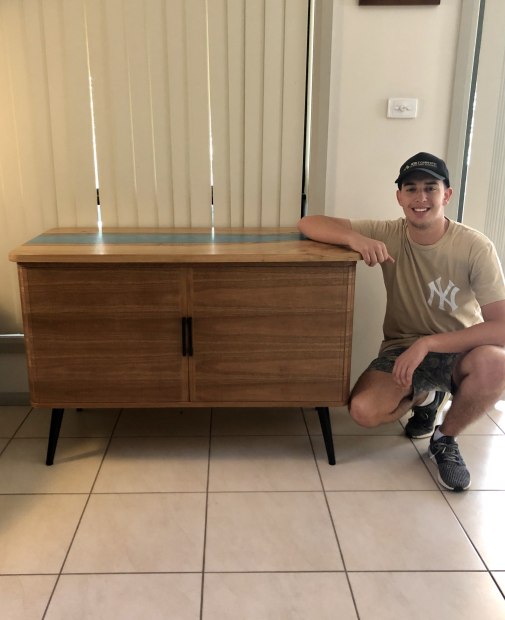
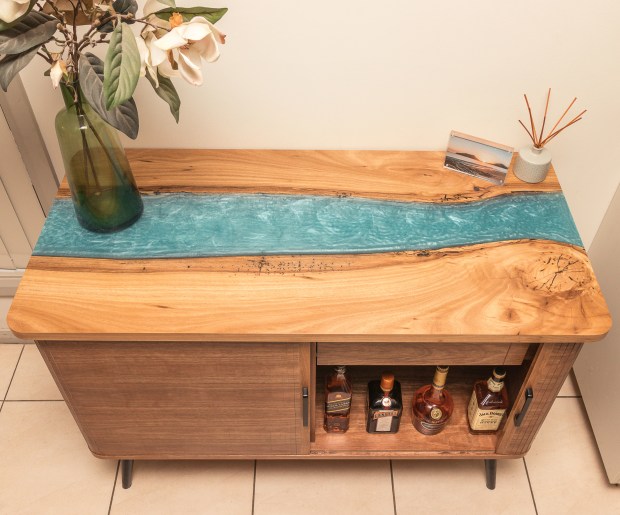
Images have been resized for web display, which may cause some loss of image quality. Note: Original high-resolution images are used for judging.